Discussing the Infrastructure Challenge
Allowing plenty of time and engaging all appropriate parties can help make the fleet depot electrification process go more smoothly.
NACFE staff interviewed 122 people leading up to Run on Less – Electric DEPOT. We wanted to present a balanced real-world view of what it takes to move from having one or two battery electric trucks in a fleet to having 15 or more. During each interview, we asked the interviewees to talk about the challenges they faced in trying to increase the number of electric vehicles at a depot. We had to dig a little to get them to share the challenges they faced, but many agreed to talk about the challenges and what they did to overcome them.
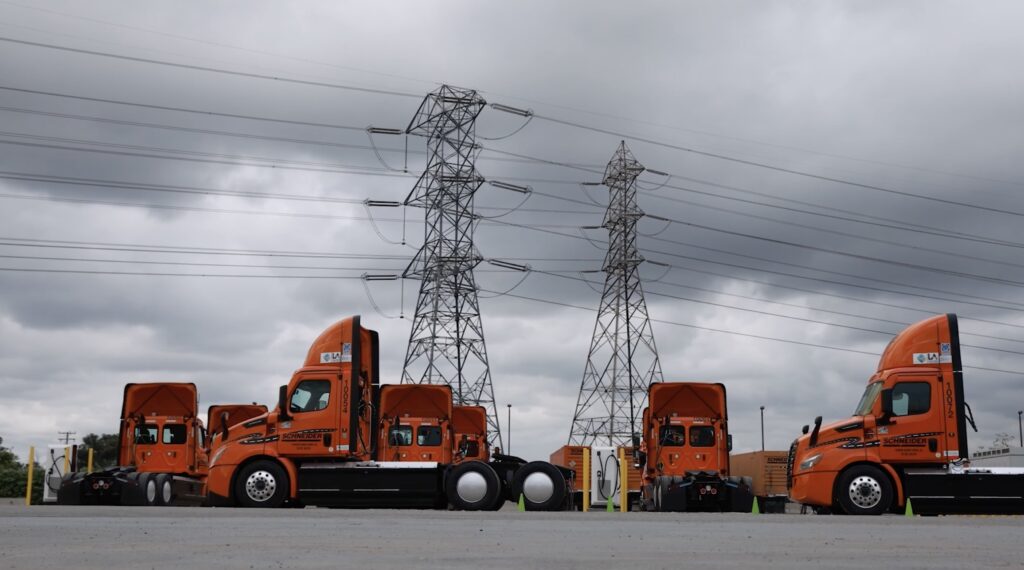
Infrastructure is often identified as one of the biggest challenges to the widespread adoption of battery electric trucks by fleets. And fleets should be concerned about the charging infrastructure if for no other reason than successfully implementing charging infrastructure takes a great deal of collaboration and time.
“I can tell you the infrastructure is a lot more in-depth than what people think,” said Charles Burton, director of fleet operations, PepsiCo Beverages North America. “It’s probably about an 18-month process from the time you say, ‘hey, I’m going to put an electric vehicle in here’ until the time you actually put an electric vehicle in service.”
Marie Brougham, supervisor, strategic account management, Sacramento Municipal Utility District, explains getting the right infrastructure is an explorative process for the utility as well as the fleet. “It’s a huge learning curve for us as a utility because we haven’t had to really be in the fleet industry,” she said.
In other words, fleets need to be prepared to spend time educating utilities about their operations. The utilities will need to know the number of battery electric vehicles (BEVs) the fleet is planning to purchase initially as well as what future purchase plans look like. They also need to understand where vehicles are currently parked, what type of chargers the fleet is planning to use and the speed of those chargers, dwell times for the BEVs, whether they will use pull-through charging, etc.
“I would love customers to do their homework up front to really understand before they cut the purchase order for those trucks,” said Adam Stadnik, transportation electrification specialist, Southern California Edison. “Customers coming to me with more fully developed projects makes my life easier because now I can just set forth, do a site assessment with my engineer and get something on paper very quickly.”
Fleets are finding ways to get their BEVs into service more quickly using temporary portable charging solutions while waiting for the permanent solutions to be constructed. “Our permanent infrastructure has not yet been installed,” said Ken Marko, fleet sustainability manager, US Foods. “However, we took the step of adding some temporary chargers or portable chargers on site. We’ve got five of them and we’re demonstrating that we can successfully operate battery electric vehicles, even with portable chargers.”
One benefit of these portable chargers is that US Foods can not only use them at the La Mirada, CA location, but also can use them on future sites where they implement electric vehicles.
Engage All Partners
Getting a depot electrification project completed involves a lot of parties. According to Tim O’Neill, EV fleet specialist PG&E, EV Fleet Team, “Fleets are juggling a charger manufacturer, they’re juggling the vehicles, they’re juggling the utility. And we’re trying to really orchestrate this where everything comes together at the same time.”
Good partnerships and good coordination are really necessary for the project to run as smoothly as possible.
Randal Kaufman, sales director, Black & Veatch, says all the parties including construction managers, project managers, subcontractors have to work collaboratively. “The great thing is everybody is equally motivated by the mission and that is sustainability, reducing pollution and the economic benefits.”
Your partners can help you understand lead times for various parts of the project. “One of the toughest things is trying to understand lead times for certain materials and equipment,” said Andrew Hicks, director of professional services, BGIS. “Having those strategic relationships in place is super critical to be able to move your project timeline along and staying aligned with that.”
For example, there’s a long lead time on certain equipment, like switchgears. “You need to work hand-in-hand with your partners to make sure that you can bring a site up within a reasonable timeframe,” said Umar Javed, president and co-founder, WattEV.
Pick The Right Locations
There are better and worse locations to implement depot level electrification. Choosing locations that are near underutilized substations, those with the ability to accept new loads, are better than choosing stations operating near capacity. Greenfield installations will tend to be quicker and less expensive than retrofitting older facilities.
“We’re really encouraging our customers as they’re thinking about electrifying to come talk to us even before they have trucks on order so that we can start talking about their plans, the capacity and ensuring that that power is available at their site,” said Justine Chao, a senior manager with Southern California Edison.
Hicks explained that a good facility manager needs to understand the role the facility plays in terms of integration with the electric vehicle charging infrastructure and equipment. “They should be able to provide good understanding of how much energy is needed and available, and what’s the capacity for adding new infrastructure and start to plan which facility might be best to deploy first.”
Expect Glitches
However, even when there is great communication and information sharing, it is likely that a problem will creep up. “I would say that every project that I’ve worked on, we’ve run into speed bumps along the way,” said Cory Skillern, clean energy technical senior advisor, Southern California Edison. “There hasn’t been one where we didn’t have speed bumps.” Despite those “speed bumps,” Skillern said that the most successful projects have been where the customer and the utility were collaborating and trying to achieve the common goal of electrifying their site.
One area that seems to slow down the process is permitting. “Permitting is a challenge for installations, but it’s absolutely necessary because it brings value to our installations,” said Brett Beard, EV Infrastructure Operations Director, Beard Electric EV. “We won’t do an installation unless it is permitted because it brings in the requirements for the customer to have a quality installation.”
Marcus Kilgo, project manager, InCharge Energy, echoes that sentiment. “One of the largest challenges that you’ll find with any project like this is going through the local municipality, getting your permit together, making sure your plan check is proper so when you go to submit it, it gets approved the first time.”
Plan For the Future
When electrifying a fleet depot, it is important to keep the future in mind. “We suggest future-proofing the site,” said Will Stearns, civil engineer and project manager, Cleantek. You don’t necessarily have to install the breakers, but you need to install conduit that is large enough to meet future needs. “Swapping out chargers with the conduit already there and just pulling the wire is much easier than having to put in new conduit.”
He explains that future-proofing is basically getting everything set into an existing switchgear and then just not running the wire.
Rebecca Roberts, department manager, e-mobility, Con Edison added, “We work to understand current and future electrification plans. We want to make sure we provide the power needed to fully electrify the fleet today, but also understand if there are any future loads that will come on board.”
Fleets can lower costs by considering future needs during the initial infrastructure project.
Advice
While there are lot of moving parts to a depot electrification project, many fleets along with their partners are successfully navigating the process and have some advice for other fleets considering adding BEVs. “My key word here is ‘patience’ as far as getting the site installed,” said Richard Rocher, account manager, Southern California Edison.
“It is extremely important to see the utility as a strategic partner in your electrification plans, and that means engaging us early in your plans,” said Chanel Parson, director of electrification, Southern California Edison. “We would like to know before you think about purchasing your vehicles really to five plus years beyond before your electrification plans.”
Ultimately, as Sean Larkin, senior director for media and heavy duty fleets at BP Pulse, said, “Every depot project is a complicated project. No one is identical to any others and each one has its little nuances and specific needs,” and you need keep that in mind for a successful implementation.